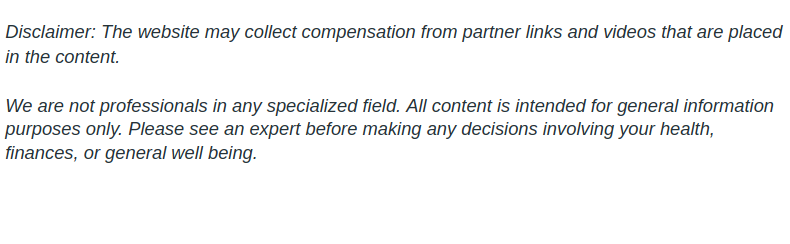

Turnkey PCB assembly makes the printed circuit board production process much easier and efficient. Electronics production companies may wish to turn to a turnkey PCB assembly method for a number of reasons:
- Many companies would rather focus on the sales and marketing of their finished product, not dwell on the processes that need to happen even before the product goes into production. Turnkey PCB assembly allows another party to take care of the PCB fabrication, then send it to the product manufacturer in order to complete the process.
- Most small to medium-sized companies and startups don’t have the budgets to purchase and install PCB manufacturing equipment or hire more engineers that are required to design effective PCBs.
-
Not only will it be more ideal from a sales and marketing standpoint — since that is all the company is actually know for — and also cost effective from an employer’s point of view, but it is less stressful on the workers.
There is less of a learning curve for existing engineers and production members when an outside party takes over the PCB manufacturing portion of product creation.
Of course there are some potential downsides to turnkey assembly. Communication being the main one. If a company is unable to communicate with their PCB manufacturer, then it is possible that there will be discrepancies throughout the manufacturing process.
When designers, engineers, and the final product company do not communicate, there are a variety of things that can go wrong, including the following:
Clearance Issues: Manufacturers have “clearance constraints,” that they must maintain between each layer of the circuit board. Often, an engineer will design a board below the minimum clearance constraint, and the manufacturer is incapable of producing a PCB with such a small constraint.
Mechanical issues: Discrepancies in part sizing can be problematic when time comes to assemble the circuit board. When component of the board do not fit together, the board will not be properly assembled. Sometimes the parts of the board will be too close to the solder, requiring the manufacturing process to be extended. The dimensions of the circuit board should be double checked preceding the first step of PCP fabrication to make sure there is ample room between each layer, pad, and track.
Drill Constraints: Similarly to clearance, PCB fabricators have drill constraints that control what the minimum and maximum size drills can be used. A typical drill size depends on the PCB’s size. Not complying with the drill constraints can increase both the cost and time it takes to create the end product.
When there is close communication between the hiring company and the turnkey PCB company, there shouldn’t be any issues. Be sure to have a thorough meeting detailing all manufacturing limitations prior to any design work or production.