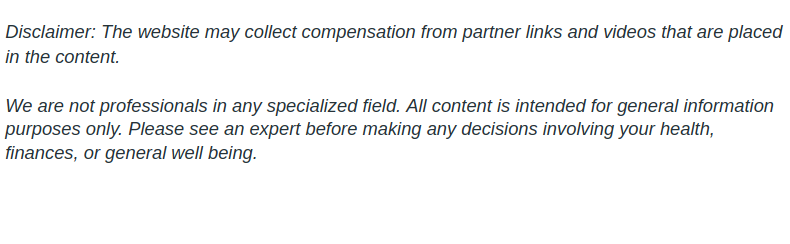

What is Thin Film Deposition?
Thin film deposition is an advanced manufacturing process that drives the entire constructions of optical devices, disk drives, solar panels, and semiconductors. This technological process produces a very thin film–so thin it is only as thick as a few atoms–of some element. The process creates alloys that can be applied as a coat to strengthen or protect another element. One of the most exciting realities of this process is that it is foundational to nanotechnology and crucial for making integrated circuits. Without thin film deposition, none of today’s advanced electronics would be possible.
How Does it Work?
Some kind of material or element is put into a vacuum furnace, and there put into a vaporous state and then brought out of that state by electricity, evaporation, chemical reaction, or high heat. The thin films of material brought out of the vapor state are used to coat or alloy another material. The process has been around for quite a while for making jewelry and other applications, but today it is done primarily in a modern vacuum furnace using, normally, a molybdenum boat or tungsten crucible. Today’s vacuum furnaces are capable of reaching incredible temperatures–above 2,192 degrees F–and are used in the medical, electronics, and energy fields, among others. The benefit of a vacuum furnace is it allows more control over the molecules vaporized off whatever element is being thin filmed, while ensuring that no molecules of any other substance mix with the one being vaporized.
What is Used to Hold the Material Being Thin Filmed?
The element being thin filmed must be held in something, normally referred to as a boat, which is strong enough to completely withstand enormous amounts of heat, strong chemical reactions, or electrical currents so that no molecules of the boat’s substance will be thrown off and mixed with the original element. But the boat must also be able to conduct heat or electricity well enough that the original material can be turned to vapor. Tungsten and molybdenum boats are among the most popular containers for this application.
Molybdenum was officially named an element in the late eighteenth century, and tungsten was discovered in 1781. Tungsten processing is popular because of the strength of this element: it is twice as dense as steel and has the highest melting point of all known elements at 6,170 degrees F. However, despite its normal toughness, tungsten does occasionally react with particular elements, so molybdenum boats are also used because this element also resists corrosion and has a high 4,748 degree F melting point.
What is This Process Used For Today?
Thin filming is still used for applications like making plated silverware, coated jewelry, or anodized aluminum. But the most exciting modern applications are in computer hard disk manufacturing and nanotechnology. With the quality of vacuum furnaces, tungsten alloy machining, and the strength of things like the molybdenum boat, chemical vapor deposition can be used to put magnetic coatings on hard discs in layers so thin they are measured in nanometers. The thinness of the layers allows huge amounts of information to be stored on a tiny surface, and there is growing interest in using chemical vapor deposition to grow carbon nanotubes.
Thin filming is a crucial process we rely on for making batteries, recording media, production of LEDs: in other words, to make many of the things we consider essential to modern life.