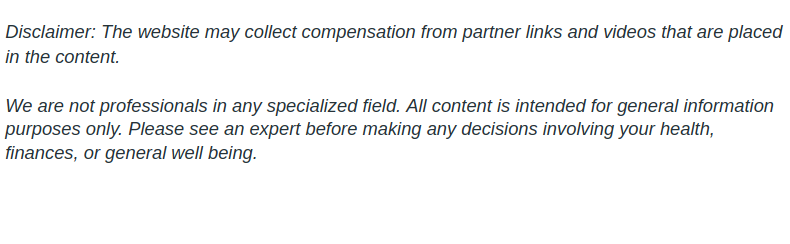

Metal coatings are integral to the manufacturing industry in the United States. Many products are completely impossible to work with without metal coatings, though these of course are not the only types of industrial coatings on the market. Low friction coatings, thermal spray coatings, and wear-resistant coatings are also among the types of coatings often applied to different materials during the manufacturing process. Most coatings ultimately end up being metal, but may function in different ways depending on what they’re being used for. Below, we’ll look into what industrial coatings are used for, what they’re made of, and how they function. While one type of industrial coating might work for certain products, others might not serve the same purposes. Let’s explore further the pros and cons of different types of industrial coatings, metal or otherwise. It’s important to remember that without protective coatings, many of the products we rely upon would be virtually impossible to use.
What Are Industrial Coatings Used For?
Metal coatings, industrial and otherwise, are used for a variety of different purposes. Sometimes, they are layered upon firearms to ensure that such weapons don’t overheat, and at the same time are usable. Without the protection of metal coatings over firearms, they wouldn’t even be touchable. For the same reasons, among others, such coatings are used on top of automobiles. Hard coatings are also used in the oil industry. Of course, these coatings vary in terms of ingredients and quality.
What Are Industrial Coatings Made Of?
The amount of ingredients involved in industrial metal coatings depend on what the particular coating in question is being made, and why. For example, when it comes to galvanized substrates, the greater the amount of zinc, the greater the protection against panel corrosion. Two of the most commonly used types of galvanized substrates are G100 and G60. Now, a G40 coating is a galvanized coating that contains 99% zinc. It’s applied to a base steel sheet utilizing a hot dipped coating process. A G100 coating, on the other hand, contains one ounce of zinc for every single square foot of panel. G60 substrates, on the other hand, contain .6 ounces of zinc. It’s important that G100 substrate has 66% more protective zinc that a G60 substrate. These are not the only types of coatings, of course.
What Are The Different Types Of Coatings?
Let’s look into three different types of coatings. Powder coatings, as the name suggests, come in a powder form rather than a liquid form. The power is applied dry and electrostatically to a metal part. The part in question is then cured under a heat of about 200 degrees Fahrenheit. The result is an appearance that is both smooth and pleasing to the eye. Then there are aluminum and metal coatings, of which there are two kinds. These include hot-dipped aluminum silicon and hot dipped metal coatings of pure aluminum. While hot-dipped aluminum silicon coatings have amazing heat resistance, withstand heats of up to 1250 degrees Fahrenheit, it also has the advantage of reflectivity. It can reflect up to 900 degrees Fahrenheit. There are also two types of high temperature coatings. The first type functions as a diffusion coating, which means that the deposited mass is diffused or reacted with a substrate. This forms a continuous gradiation in composition. The second type is actually an overlay coating — it’s deposited at the surface of the substrate.
What Is The Market For Industrial Coatings?
Industrial coatings are used not only in the products mentioned above — it can be overlaid over traffic marking paint, and it’s actually in high demand. At $1.3 billion in 2014, industrial coatings make up the second largest sub-segment. It’s a hugely valuable, and the variety with which these materials can be used only increases that value.