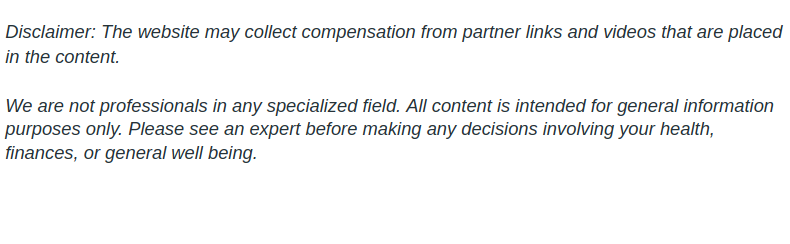

Due to the inherent risks present on many different types of job sites, OSHA has very clear rules and regulations for companies on ways they are required to provide their employees with a safe working environment.
OSHA focuses on planning, providing, and training as the three-step process to avoid workplace injuries. Planning includes understanding the risks associated with the job, mitigating as many of those risks as possible, and planning out what safety measures can be put in place throughout the job.
Providing refers to providing all employees with the necessary safety equipment to protect them in the event of an accident like a fall. OSHA provides regulations on the various heights workers are allowed to work before safety gear has to be provided. In the construction industry, it is six feet off the ground. All workers six feet or more above the lower level must be provided with fall protection gear. In the general work industry, the requirement is at four feet, and in shipyards, the requirement is at five feet.
A fall doesn’t have to be significant for an injury to happen. There are many different types of fall protection gear including hook rigging, slings, crane service, and lifting gear.
The third step in OSHA’s process is training. Companies have to ensure their employees are properly trained on the safety ways to accomplish their job and best practices for avoiding accidents. This includes rigging training and rigging certification. The rigging equipment can be complex particularly for an untrained employee, which can open the entire crew up to the potential for injuries.
Some workers may think the OSHA regulations are simply red tape and unnecessary. However, the regulations put in place for employee safety are based on research, past events, and best practices. Studies show that feeling safe in the workplace is important to employees, yet many do not feel comfortable drawing attention to unsafe measures to their supervisor or coworkers.
Thousands of people are injured or become ill each year due to their workplace environment. Slips and falls are the most common types of injuries. However, they are the only types. There are a lot of different ways workers have been injured on the job, and OSHA works to use their incidents as learning points to avoid future injuries.
Companies are required to provide safety gear so that price does not become a determining factor on whether or not an employee takes the necessary steps to stay safe while working. Low-income workers deserve the same protection as all workers.
Fall protection training also protects employees from the actions of other employees. One individual acting in an unsafe many can put their coworkers at risk as well. This creates an unsafe working environment for everyone on the job site. This can be avoided through consistent and ongoing safety and fall protection training.
Another important factor is the attitude of the job site supervisors. It is essential that all the supervisors treat workplace safety as important as it is, so employees know to take their training seriously and to wear their protective gear.