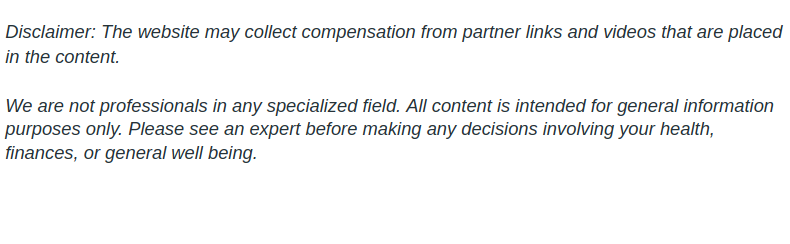

The er collets that are made today are the most widely used clamping system in the world. They are made from Alloy spring steel and hardened completely, having a run out of .0003 inches or less.. They are ideal for machine applications like boring, milling, reaming, tapping, and grinding.
Collets are not something that average people walking do the street or traveling to work in their cars are going to be familiar with. Collets are a subtype of chuck that forms a type of collar around an object to be held. A collet exerts a very strong clamping force on an object when the collet is tightened. This clamping force, when tightened is typically by means of a tapered outer collar. There are several uses for a collet. Often it is used to hold a type of tool or a workpiece.
Manufacturing purchases occur virtually every day of the week. They are purchases that involve tools and supplies to keep a specific manufacturing business going. Things like drills, drill bits, and clamps are sold and bought many thousands of time over the course of the year. Of those who make manufacturing purchases for companies, 70% of them will do so at least three times per week throughout the year. Most of the manufacturing purchases are influenced by at least three people in the company that is buying. They look for quality and durability. They look for instruments that will get the job done, not only in the short-term but in the long-term, as well.
The er collet was patented in the year 1973 and is the most widely used clamping system in the world today. The er collets are available from many different companies throughout the world and are offered in many different standard sizes that correlate to the letters ER and a number. The number refers to the cavity opening in millimeters. The E of the ER came from the original E collet. That collet was then modified by Rego-Fix and thus the er collets were born.
There are many users of a collet who might be familiar with them as part of an x-acto knife or one equivalent to it. The collet it the part of the knife that holds the blade after being tightened into place. Where the user wants to take the knife blade out, they simply unscrew the collet and slide the blade back out. This way, the blades can be stored safely. Another common example of this technology is its use in a Dremel, where the bits are held together by the screwing mechanism. After use, the bits are loosened and screwed out.
In general, collets have a clamping range that is narrow. There are a large number of collet types that are required to hold a range of bits, depending on the project. This often makes them unsuitable for general usage in electric drills and the like. However, the collet’s advantage is that it combines traits into one chuck. This is very useful for highly repetitive work.