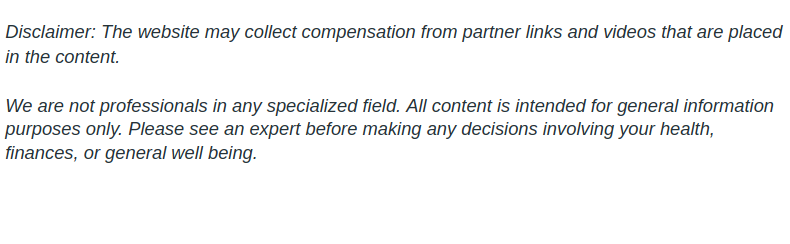
As long as there has been manufacturing in the world, there has been a need to refine the tools and items being manufactured. A freshly built product may have some imperfections on it, especially metal, and those imperfections can and should be removed. A manufactured product may be defective or make the customer unhappy if metal burrs are found on it, so lathes and carbide tool grinders are used in industries across the United States and beyond. Carbide grinders and other lathes are the solution for rough and ugly metal imperfections like burrs, and these lathe machines have a number of components to them. There’s the grinding surface itself, of course, and an assembly for holding the machined item steady during this work. Most often, a vise is being used. An interested customer can find a Kurt vise for sale, for example, if they need to update or repair their lathe. Finding a Kurt vise for sale may mean looking to one’s own supplier, or searching online such as “Kurt vise for sale Los Angeles” or “lathe Kurt vise for sale Boston MA.” What is there to know about lathes and machining work today?
The Work of Lathes and Carbide Grinders
The use and concept of lathes is hardly new. In fact, some of the oldest known lathes were some hand-operated models found in archeological digs in Egypt. Modern lathes, meanwhile, are powerful and mechanical devices that have to handle industrial levels of work. No hand-operated lathe will do the job when car parts or other pieces of metal need to be worked on. Rather, today’s carbide grinders are a sort of table with many components, some for holding the machined item in place, others for the actual grinding work.
The good news is that today’s carbides and lathes are more accurate and finely controlled than anything that has come before them. Modern lathes are built with carefully-designed parts, and they also have computers in them that can be programmed for even more precise work during machining. When a worker starts using a modern lathe, they will tell the machine what “part zero” is before starting the lathe work. Part zero, in short, is the datum corresponding to the 0,0 coordinate in the CAD drawing that was used for CAM work, or to generate the g-code part of the program. All of this ensures accurate work, since the operator would not want to accidentally grind off too much material and compromise the quality of the metal being machined. Erroneous calibration may also mean that not enough material is ground off, and that makes for an incomplete job.
Given that a lathe or carbide grinder is indeed calibrated just right, the device will activate its grinding surface, which spins at a high RPM. How fast, exactly? This may in fact vary based on the work being done. Lathes can be set to have their grinding surfaces rotate as slowly as 50 RPM or as fast as 1,800 RPM. Slower RPMs have their uses for when the item is being counter-bored, counter-sunk, or reamed. Whatever the speed, the lathe will start “feeding” the machined item to the grinding surface for work, smoothly and steadily. Feeding is simply how the machined item is pushed toward the grinding surface, and it is involved in all lathing. The machined item will be fed to the grinding surface until it has been machined to the operator’s satisfaction, and the job is done. Metal burrs and other imperfections will be ground right off, leaving only a smooth and flawless surface.
Metal Burrs
Why are metal burrs being removed, and where do they come from? Those new to manufacturing will soon discover that typical work such as drilling holes, welding, and cutting metal creates upraised, rough imperfections in the metal. These are metal burrs, and they are trouble. If left in place, burrs may scratch or scrape other surfaces of the product or others during use, causing damage. Metal burrs may also attract static electricity, a hazard for electric products. When cutting, welding, or drilling creates these burrs, they can and should be ground off to prevent those issues and also make a professional-looking item. Leftover metal burrs can make for unattractive, sloppy-looking finished products.