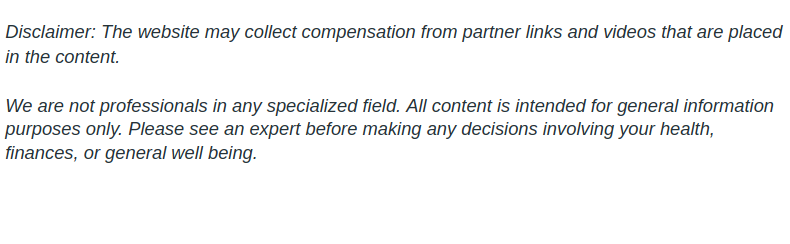
Working faster means having to work smarter. Just because something takes a long time doesn’t mean time itself is being valued. Just take a look at the construction industry.
Buildings are often seen as time-consuming tasks. You have to gather up a skilled workforce, gather up dozens of different materials, and set aside plenty of time for everyone to get the job done right. When this isn’t done to perfection it can end up wasting a lot of finite resources. In-plant modular offices are set to change all of this. Providing a high-quality result in half the time, the modular warehouse office (or in plant office) is taking the construction world by storm.
It doesn’t matter if you need a new hotel or a new series of office spaces for your workers. In-plant modular offices will leave everyone happy.
Let’s get some misconceptions out of the way first. A sturdy, high-quality building doesn’t need to take months and months to finish. You also don’t need to pay out the nose for materials and labor. Modular methods allow for speedy construction times while still putting quality at the forefront — between 60% and 90% of all prefabricated construction occurs in a warehouse or factory, offering you reliability in a pinch. They’re also one of the most environmentally sustainable options out there.
The green benefits of your company have a ripple effect. They impact your workers, affect your customer base…even the economy you work in will change. It’s estimated 90% of engineers, 85% of contractors, and 75% of architects use modular construction today. A popular reason why it’s pulled out time and time again are the environmentally sustainable benefits — according to UK-based WRAP (or Waste And Resources Action Programme), modular construction significantly reduces waste materials. These include cement, concrete, wood pallets, shrink wrap cardboard, bricks, timber, and plasterboard.
It’s not just reducing material waste, either. There’s less labor that goes into the act of making a warehouse, building, or office space. Recent studies have shown modular constructions reduce energy consumption during the building process by 65%, which will then go on to reduce energy costs for occupants. It’s a green rolling effect that just keeps picking up speed the more time goes on. A recent report by the Building Industry Association Of Philadelphia estimates going modular will reduce construction costs by 10% or more.
Take a look at any industry and you’ll find in-plant modular offices dominating in some form. Hotels, in particular, are leading the pack with their latest innovations — Marriott International pledged to modularly construct up to 15% of its North American developments in 2017. A few years back in 2011 modular construction was considered a must-have for commercial applicants. Nearly 50% of respondents to a survey on new buildings stated they used modular processes for healthcare facilities, dormitories, and college buildings. What could portable warehouse partitions do to save you some money?
Out with the old, into the new. There’s no reason to stick around with obsolete methods that don’t yield long-term results. Modular constructions — be they prefabricated offices or new apartment complexes — are one of the most energy-efficient building methods around. They can be constructed on less labor and less time, allowing workers to expend their energy on other tasks. They use up far less materials, to boot, and provide the environment with some much-needed relief.
Work faster, work smarter. Apply for in-plant modular offices that save everyone materials, time, and money in the long-term.