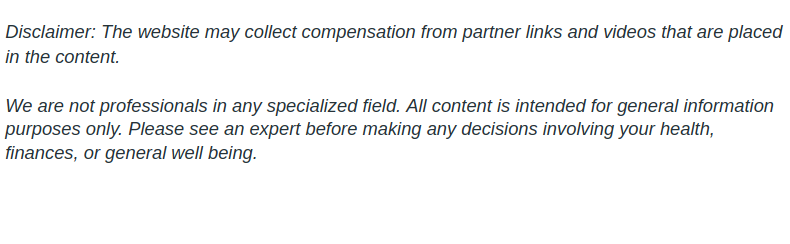
A ceramic coating can help safeguard any surface on which it’s applied, especially if it’s applied in the right way. The coating price will differ depending on specifics such as the manufacturer and the roles that the coating plays. You should learn about the various types of ceramic coating that are available on the market, as well as what each one of them does. With the necessary knowledge, you may also find it easier to hire the right people to do the job because you’ll have an idea of the questions that you need to ask them.
Find out from reviews and people you may know who have used ceramic coatings for the purpose that you need it whether they can make any recommendations. This will enable you to tell apart a professional coating and one that isn’t so that you make a worthwhile investment. If you can get the right people to do the job for you, you can be sure that your ceramic finish is going to serve the intended purpose perfectly. You may also be able to save a lot of time and money since quality ceramic finishes are some of the most durable finishes that you can find.

Kilns can be used for a wide variety of important purposes. Kilns can make beautiful art, of course, but they can also be used to make things that are useful in day to day life. Providing a high temp ceramic coating kit is one thing that just about any kiln will be able to do, though it is important to mention that high temp ceramic coating kits will vary from usage to usage, and an ITC ceramic coating comes in a number of different varieties.
In fact, there are five different types of ITC ceramic coatings in general, though most of them could still be considered to be an ITC high temp ceramic coating, as this ITC high temp coating is highly useful for a wide variety of different applications. For instance, the ITC 148 is one type of coating, as is the ITC 100HT ceramic coating. In addition to this, the ITC 213 ceramic coating is designed to be specifically used on metals that often do not work well with any other type of high temp ceramic coating. In addition to this, the ITC 296A is yet another type of high temp ceramic coating, one that is predominantly used as a top ceramic coating.
Of course, even the most high temp of ceramic coatings can sustain damage over the course of time. Depending on the type of ceramic coating, this will be more prevalent in some objects than in others, something that will also depend on the use of the object in question. For the purpose of repairing these ceramic coatings, ITC 200 EZ ceramic repair is there to help. This ITC 200 EZ ceramic repair can be used in a number of different ways, but it will be able to give new life to just about any ceramic coated object that is perhaps in need of a little TLC in order to look like new again (or at least close to it).
But when we consider the use of the typical high temp ceramic coating, we must also consider the kiln that it will be fired in. Using a high temp ceramic coating but not using the kiln itself properly is far from likely to give you the ideal results that you are looking for, and might even destroy the product that has had the high temp ceramic coating applied to it completely, meaning that whoever is producing this product will need to start over from scratch, something that can be costly as well as time consuming, particularly if it keeps happening over and over again due to improper usage.
For instance, the placement of the object with the high temp ceramic coating (or really just any object, at that) is absolutely critical. It is currently recommended that objects be placed further than one and a half inches away from all kiln elements, centering the object somewhat inside of the kiln. The placement of an object might seem like somewhat of a small thing, but it is a small thing that can have a considerable impact in the final outcome of the product in question, particularly if it has been given a high temp ceramic coating.
And any kiln that is in use should also be provided with regular servicing and maintenance in order to keep it in good shape. For instance, kiln elements do not last forever, something that not everyone is aware of (particularly if you do not work directly with kilns, of course). Kiln elements will develop a resistance over the course of time and once this resistance reaches around nine percent, it is typically recommended to change them out for new ones. Typically, these elements will be ideal for use for only around one hundred firings. Keeping them in longer than that can actually damage and change the overall outcome and quality of the products that you fire within your kiln, something that can have a hugely detrimental impact, to say the least.
From the high temp ceramic coating to the well cared for kiln, there are many applications for such things all throughout the United States. However, taking precautions in both is necessary to get the desired outcome you want.